MSU researchers helping low-volume meat processors determine wastewater treatments
Two projects to help small meat processors manage wastewater have been funded by the Michigan Alliance for Animal Agriculture.
EAST LANSING, Mich. — Local meat processing facilities, particularly small businesses that work with a relatively low volume of processing, are vital contributors to the food supply chain in many communities across the country.
One of the primary challenges they face is how to manage the wastewater produced from their operations.
The issue has been brought to the national forefront in recent years, as the U.S. Environmental Protection Agency examines the environmental effects of wastewater from the meat processing industry.
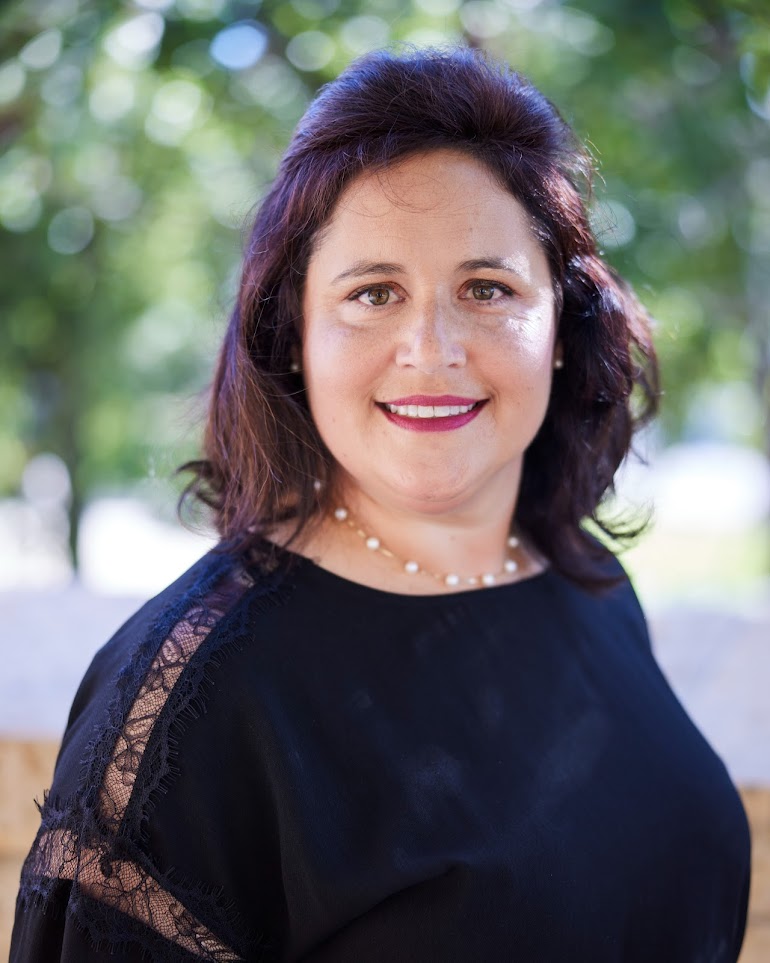
In Michigan, these low-volume facilities often rely on decentralized wastewater treatment due to cost and lack of access to municipal centralized options. They frequently must obtain a groundwater discharge permit from a state or regulatory agency, such as the Michigan Department of Environment, Great Lakes and Energy (EGLE).
Current methods typically involve pretreatment systems, followed by biological treatments and finally land application. Pretreatment is often through storage in septic tanks, which separates any solids from wastewater.
There are multiple biological treatments, including various types of lagoons that hold wastewater for a predetermined period of time to treat it. Anaerobic lagoons rely on bacteria to treat wastewater, while aerobic lagoons use algal growth and microorganisms, as well as aeration. Facultative lagoons utilize both aerobic and anaerobic elements.
Finally, land application depends on soil to take up wastewater and further break down components.
To gain a better understanding of the effectiveness of these strategies, Michigan State University researchers and Extension educators have received funding for two projects thus far from the Michigan Alliance for Animal Agriculture — a partnership among MSU, the Michigan Department of Agriculture and Rural Development, and animal agriculture industry groups.
The initial research featured Steven Safferman, a professor in the Department of Biosystems and Agricultural Engineering (BAE), who has since taken a new position outside of the university. Younsuk Dong, an assistant professor and irrigation specialist in BAE, has joined the team for the ongoing research.
Other scientists include Gregory Rouland, a graduate research assistant who worked with Safferman and is now a member of Dong’s laboratory, and Andrea Garmyn, an academic specialist with the Department of Food Science and Human Nutrition.
Jeannine Schweihofer, now the associate director of MSU Extension’s Agriculture and Agribusiness Institute, was formerly a senior meat quality educator and has been involved in the project throughout.
“There are relatively few options for low-volume meat processors when it comes to wastewater,” she said. “The ultimate goal of this research is to provide processors with cost-effective wastewater management strategies while protecting groundwater and the environment.”
For the first project, which had results published in the journal Water in early 2024, six Michigan processors were selected in an effort to characterize the wastewater they produce. The facilities were chosen based on several criteria, including the type of meat processing and currently implemented wastewater management procedures.
Various samples were collected at each facility at six different times over the course of a year and screened for total nitrogen, ammonia, nitrate, phosphorus and other compounds.
The team found that multiple samples were required to get an accurate depiction of wastewater contents. Schweihofer said that an annual sampling will not yield accurate enough results on which to base decisions.
“Samples need to be taken as close as possible to the time of discharge to be accurate for what is actually being discharged,” she said. “For example, if we take a sample a month after a lagoon is emptied, then the lagoon doesn’t have time to do its job and the levels will be high. But that isn’t what is being discharged.”
To adhere to newer standards, researchers suggest a number of potential solutions. These include pretreatment in multiple lagoons to allow more time for the breakdown of compounds, adding aeration or filters, and gaining a better understanding of soil capacity to ensure the soil can deal with the volume of wastewater.
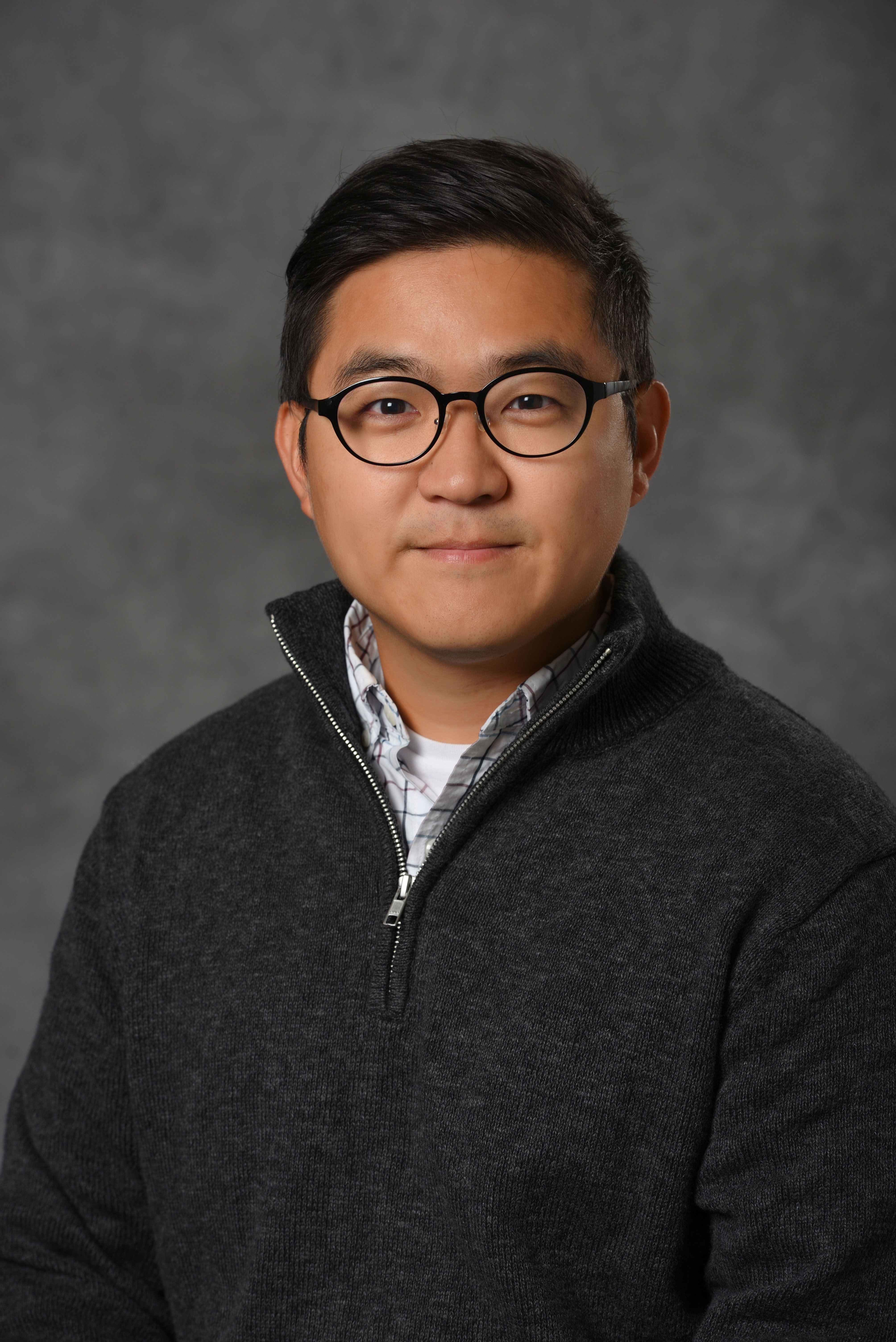
Finding cost-effective solutions is important for Dan Swartzendruber, president of the Michigan Meat Association. He said the permit requirements established in 2020 can be challenging for producers.
“Many of the small processors are fighting to remain in business with the rising costs,” he said. “With the new permit mandates, it may force these processors to invest in water treatment systems that will cause them to either close their plants or face long-term debt that would prevent them from being able to offer competitive wages and benefits to their employees.”
The second project is ongoing and addressing site-specific needs for processing facilities, taking into account that some approaches are more appropriate than others depending on location, processing techniques or facility features.
Researchers are evaluating an assortment of treatment and discharge methods, developing a decision-support tool for producers to determine which option is ideal for them, and identifying best practices for wastewater reduction and management.
“The results from our initial work indicate that even simple decentralized wastewater treatment systems that use techniques such as aeration and filtration, combined with facility management practices, can substantially reduce or improve permitted wastewater characteristics,” Schweihofer said. “We know that small business owners are always looking at how new practices affect their bottom lines, and we also know that needs are different for each producer. We want to show that there are strategies that make economic sense, in addition to improving the industry’s sustainability.”
Swartzendruber is happy with the research progress and anxious to see the continued results.
“On behalf of producers and the industry, I’m very interested in the continuation of these research efforts to find out what the true costs are,” he said. “I know we’d all like to learn what other options could be available to processors that are not currently listed in the permit but may be effective.”
Michigan State University AgBioResearch scientists discover dynamic solutions for food systems and the environment. More than 300 MSU faculty conduct leading-edge research on a variety of topics, from health and climate to agriculture and natural resources. Originally formed in 1888 as the Michigan Agricultural Experiment Station, MSU AgBioResearch oversees numerous on-campus research facilities, as well as 15 outlying centers throughout Michigan. To learn more, visit agbioresearch.msu.edu.